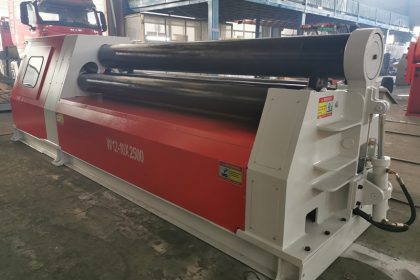
What are the advantages of the four-roller sheet metal bending machine compared to the three-roller sheet metal bending machine
The sheet metal rolling machine is a kind of public forging machinery and equipment that can bend non-metal sheet into cones, spheres, cylinders or other shapes. This performance is widely used in manufacturing, boiler steam, chemical industry, Non-metallic structures and machine building and other businesses. The four-roller sheet metal rolling machine is suitable for the bending and forming of sheet metal. It can roll round, arc and tapered workpieces within a certain range, and has the function of pre-bending the end of the sheet. The remaining straight edges are small and the work efficiency is high. , And the metal sheet can be roughly leveled on this machine.
The three-roller sheet metal rolling machine and the four-roller sheet metal rolling machine have different roller motion forms. But their working principles are the same, they all use the principle of three-point fixed circle to roll different radii. The difference between the four-roller sheet metal bending machine and the three-roller sheet metal bending machine is as follows:
1. The English name of the three-roller sheet metal bending machine is called (3 roller bending machine or Three roller stee plate bending machine). The upper roller is symmetrically positioned at the center of the two lower rollers, and the hydraulic oil in the hydraulic cylinder acts on the piston to move vertically. The final gear of the main reducer drives the gears of the two lower rollers to mesh and rotate to provide torque for the rolled plate. The four-roller sheet metal rolling machine is suitable for the bending and forming of sheet metal. It can roll round, arc and tapered workpieces within a certain range, and has the function of pre-bending the end of the sheet. The remaining straight edge is small, and the work efficiency is small. High, and the metal sheet can be roughly leveled on this machine.
2. Three-roll asymmetric metal plate bending machine, the upper roller is the main drive, the lower roller moves vertically to clamp the plate, and the lower roller gear meshes with the upper roller gear, and serves as the main drive at the same time; the side rollers are tilted Lifting movement, with dual functions of pre-bending and rolling. Compact structure, convenient operation and maintenance. The upper roller of the four-roll sheet metal rolling machine is the main drive, which is connected with the upper roller through the reducer and cross slider coupling to provide torque for the rolled sheet; the lower roller moves vertically through the reducer worm gear (bevel gear). ) Obtained by the nut and screw pair, in order to clamp the plate, for mechanical transmission; side rollers are arranged on both sides of the lower roller and tilted along the rack guide rail, through the nut and worm worm gear (or bevel gear) With transmission; all four work rolls adopt rolling bearings.
3. When the four-roller sheet metal rolling machine is working, the position of the upper roller is fixed and the lower roller moves upward to clamp the steel plate in a straight line. The rollers on both sides move in a straight line or arc to move closer to the roller to adjust the radius of curvature of the reel. The English name of the four-roller and three-roller sheet metal bending machine is called (3 roller bending machine or three roller stee plate bending machine). The roller motion forms are different, but the working principle is the same. They all use the principle of three-point fixed circle. Rolling of different radii. However, the pre-bending straight edge and roundness of the roundness of the four-roll sheet metal bending machine are better than those of the three-roller.
The sheet metal rolling machine is a kind of public forging machinery and equipment that can bend non-metal sheet into cones, spheres, cylinders or other shapes. This performance is widely used in manufacturing, boiler steam, chemical industry, Non-metallic structures and machine building and other businesses. The four-roller sheet metal bending machine is suitable for the bending and forming of sheet metal. It can roll round, arc and tapered workpieces within a certain range, and has the function of pre-bending the end of the sheet. The remaining straight edges are small and the work efficiency is high. , And the metal sheet can be roughly leveled on this machine.
The four-roller sheet metal rolling machine is composed of four rollers. The upper roller is mainly driven and the position of the upper roller is fixed. The two ends of the lower roller are driven by hydraulic cylinders. The lower roller can be raised to clamp the head of the plate with the upper roller, and the distance between the side roller and the upper roller can be changed as needed to bend the heads at both ends of the plate. Then the lower roller is lowered, the two side rollers are raised, and the sheet is rolled into a cylindrical shape. Any machine must be operated correctly in accordance with the process requirements. Let’s talk about the correct operation method of the four-roller sheet metal bending machine.
Generally prepare from the following aspects:
1 Clarify machine functions
The sheet metal rolling machine is a kind of public forging machinery and equipment that can bend non-metal sheet into cones, spheres, cylinders or other shapes. This performance is widely used in manufacturing, boiler steam, chemical industry, Non-metallic structures and machine building, etc.
2 Understand the working principle of the machine
The four-roll sheet metal rolling machine and the three-roll sheet metal rolling machine have different roller motion modes, but the working principle is the same, and they both use the principle of three-point fixed circle to roll with different radii. The position of the upper roller is fixed, and the lower roller moves upward linearly to clamp the steel plate. The rollers on both sides move in a straight line or arc to move closer to the roller to adjust the radius of curvature of the reel.
3 Familiar with operating procedures
(1) The sheet metal rolling machine must be managed by a dedicated person.
(2) The operator must be familiar with the structural performance and use of the sheet metal rolling machine, and the operation can only be carried out with the approval of the responsible manager.
(3) Check carefully whether the safety device is in good condition before starting the machine.
(4) During operation, it is strictly forbidden to put hands and feet on the rollers, transmission parts and workpieces.
(5) After work is interrupted, the clutch should be turned to neutral.
(6) Multi-person collaborative operations must be directed by a dedicated person.
(7) Overwork is strictly prohibited.
(8) The tilting reset of the lifting and turning bearing of the upper roller and the balancing of the upper roller must be carried out after the main drive is stopped.
(9) It is forbidden to pile up workpieces and sundries in the workplace, so as to keep the machine tool and the site clean at all times.
(10) After the operation is completed, the power supply should be cut off and the power supply box should be locked
The four-roller sheet metal rolling machine is an important equipment in the production of enterprises. You must operate it in the correct way during use, otherwise not only the equipment will be damaged and the production will be affected, but also unexpected consequences will occur.