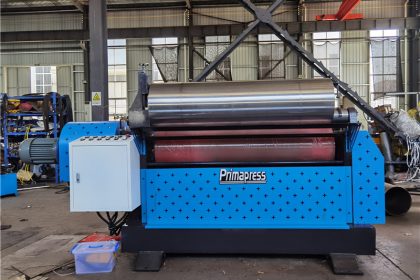
Understand the advantages and disadvantages, processing methods, and processing principles of the two-roller plate rolling machine
Understand the advantages and disadvantages of the two-roller plate rolling machine
The advantages of the two-roll plate rolling machine:
- The two-roll coil winding machine has a fast processing speed;
- The two-roller plate coiler performs high-precision forming in one stroke;
- Even if the slab is processed by punching, cutting, embossing, etc., it will not produce cracks and irregular warping;
- The slab of thetwo-roller plate rolling machinewill not wrinkle the slab and cause scratches on the surface of the workpiece;
- If the rolling volume of the double-roller plate rolling machine is large, even if the distance between the two rollers changes and the diameter of the part does not change, the equipment accuracy is not very high, and simple equipment is used, etc.
The disadvantages of the two-roll plate rolling machine are:
- The two-bar rolling mill is not suitable for multi-variety and small-batch production, because each time the two-bar rolling mill changes relative to the product diameter, it is necessary to make guide rollers;
Can not do thick plate processing (maximum processing plate 6-9mm).
Demystifying the processing method of the two-roll plate rolling machine
Two-roll plate rolling machine can roll metal plates into circular, arc and conical workpieces within a certain range. The plate coiler is a work roll type equipment that bends and forms the plate. It can form parts of different shapes such as cylindrical parts and conical parts. The length is often an important processing equipment.
The two-roller plate rolling machine acts on the center symmetrical position of the piston. The two low rollers pass through the hydraulic oil of the hydraulic cylinder, and the two lower rollers gear and the driving rotation cooperate through the main transmission gear of the main reducer to provide torque for plate rolling. There are two types of two-roller plate rolling machines: mechanical and hydraulic: mechanical two-roller plate rolling machines are divided into symmetrical machines and asymmetrical machines.
The flat plastic metal sheet passes through the rotary motion of the upper roller and the lower roller with the help of the work rolls (two rolls, rolls) between the three rollers. required cylinder, conical cylinder or a part of them. The working principle of the plate machine is to make the work rolls move through the action of liquid pressure, mechanical force and other external forces to bend or bend the plate.
The structure and operation principle of the two-roll plate rolling machine
The two-roll plate bending machine is a kind of equipment that bends and forms the plate with work rolls. It can form parts of various shapes such as cylindrical parts and conical parts. It is a very important processing equipment. The working principle of the plate machine is to make the work rolls move through the action of liquid pressure, mechanical force and other external forces to bend or bend the plate. According to the rotation movement and position changes of different shapes of the work rolls, elliptical parts, arc parts, cylindrical parts and other parts can be processed.
The upper roller of the two-roller plate rolling machine acts on the piston, and through the hydraulic oil in the hydraulic cylinder, the vertical lifting movement is performed at the symmetrical position between the two lower rollers. The final gear of the main reducer drives the two lower rollers to rotate together to provide torque for medium and heavy plate rolling. Machine Specifications The flat plastic metal sheet is rolled by three work rolls with the help of bending rolls (two rolls, one roll) and the rollers are rotated to make the metal sheet go through multiple continuous bending (lining compression deformation and intermediate, outer tensile deformation), For permanent plastic deformation, rollers require cylinders, cones or parts of them. The disadvantage of this hydraulic three-roller is the need for other equipment to pre-bend the plate ends. This coiler is suitable for large coilers with thickness greater than 50mm. A row of fixed idlers is added to the bottom of the two lower rollers to shorten the distance between the two lower rollers, thereby improving the precision of the rolled workpiece and the performance of the whole machine.