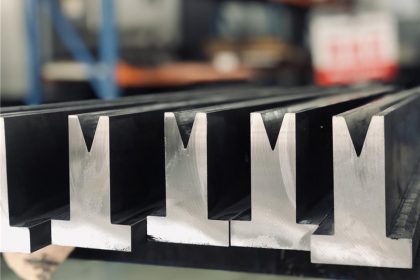
Technological Development of sheet metal cnc press brake bending machine Dies tools mold
The sheet metal cnc press brake bending machine mold manufacturing industry is also one of the industries with a large usage of CNC sheet metal cnc press brake bending machine molds. It has become a major user in the CNC sheet metal cnc press brake bending machine mold industry, such as automobiles, high-speed trains, and general machinery manufacturing.
The aerospace industry is a traditional and important application field for CNC sheet metal cnc press brake bending machine molds. In this industry, CNC sheet metal cnc press brake bending machine molds are generally used to bend aircraft structural components. These structural components are generally larger in volume, and in the past, aluminum alloys were extensively used. With the expansion of the application fields of titanium alloys and composite materials, the requirements for CNC sheet metal cnc press brake bending machine mold processing are also increasing.
From the development history of CNC sheet metal cnc press brake bending machine molds, from the late 19th century to the mid-20th century, high-speed steel was the main representative of CNC sheet metal cnc press brake bending machine mold materials. In 1927, Germany first developed a hard alloy CNC sheet metal cnc press brake bending machine mold material and obtained widespread application. In the 1950s, Sweden and the United States respectively synthesized synthetic diamonds, and the cutting of NC sheet metal cnc press brake bending machine dies entered a period represented by superhard material. In the 1970s, polycrystalline diamond (PCD) was synthesized using high-pressure synthesis technology, which solved the problem of scarce and expensive natural diamonds, and expanded the application range of diamond CNC sheet metal cnc press brake bending machine molds to various fields such as aviation, aerospace, automotive, electronics, and stone materials.
The selection of mold materials for CNC sheet metal cnc press brake bending machines is the foundation for successful bending processing. Compared with hard alloy, the mold speed of PCD CNC sheet metal cnc press brake bending machine can reach 4000m/min, while hard alloy is only 1/4 of that. In terms of lifespan, PCD CNC sheet metal cnc press brake bending machine molds can generally increase by 20 times. From the surface quality processed, the effect of PCD is 30% to 40% better than that of hard alloy. In addition, the development of CBN (vertical boron nitride) superhard material CNC sheet metal cnc press brake bending machine die and surface coating CNC sheet metal cnc press brake bending machine die also contributed to the advancement of cutting technology.
For CNC sheet metal cnc press brake bending machine molds, there are three key factors: cost, lifespan, and efficiency. Experiments have shown that if the cost of CNC sheet metal cnc press brake bending machine molds is reduced by 30%, the overall cost will be reduced by approximately 1%; If the lifespan of the CNC sheet metal cnc press brake bending machine mold is increased by 50%, the overall cost will be reduced by approximately 1%; However, if cutting parameters are optimized as much as possible and the machining efficiency of CNC sheet metal cnc press brake bending machine molds is improved by 20%, the overall cost of a workpiece can be reduced by more than 15%.