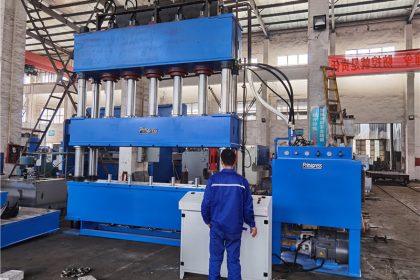
Several common problems and solutions of four-column hydraulic press machine
How to assemble the four-column hydraulic press machine correctly?
When assembling the four-column hydraulic press machine, apply oil on the lip. There should be no burrs, notches or scratches on the shaft. The shaft and hole ends should be chamfered or rounded. The machining accuracy, surface roughness and geometric position accuracy of the hole must meet the requirements; the pressure head of the four-column hydraulic press machine should be flat, but the oil seal should not be directly hit with a wooden hammer, and the deviation of the oil seal in the radial direction should not exceed 0.25mm. The end of the oil seal should be perpendicular to the hole; the pressure head or tool should not be smaller than 0.25mm than the hole diameter, only the outer part of the oil seal is allowed to be pressed, and the inside of the skeleton and other parts are not allowed to be pressed. The inner diameter tolerance of the hole must be strictly controlled when the oil seal is fixed in the hole.
Prevent the shaft end face of the four-column hydraulic press machine from vibrating, and the oil seal is damaged due to eccentricity with the shaft. Lubricate properly and in time, and there should be no dust and impurities between the shaft and the oil seal. Moreover, the price accuracy and position accuracy of the four-column hydraulic press machine shaft should be appropriate to avoid working conditions reaching critical conditions. , We must be careful and patient in the assembly process, especially in high-speed operation, all must meet the technical requirements; reduce the installed power of the four-column hydraulic press machine, reduce the energy loss in the work of the four-column hydraulic press machine, reduce noise, improve the sealing quality, and reduce the leakage of hydraulic oil. pollution of the environment.
How to disassemble the hydraulic cylinder in the four-column hydraulic press machine?
- Before disassembling the hydraulic cylinder of the four-column hydraulic press machine, first remove the hydraulic circuit, then cut off the power supply, and then remove the hydraulic cylinder after the hydraulic device completely stops rotating. Remember that the order of operations in this environment cannot be reversed.
- When disassembling, prevent damage to the top thread of the piston rod of the four-column hydraulic press machine, the thread of the oil port, the surface of the piston rod, the inner wall of the cylinder liner, etc. In order to prevent the slender parts such as the piston rod from being bent or deformed, the iron wire should be used to trap the suspension, and the cylinder should be balanced with the support of the skid.
- When removing the hydraulic cylinder from the four-column hydraulic press machine, the parts should be carefully inspected to determine the parts that need to be repaired or replaced.
Finally, it should be emphasized that in the whole process of disassembling the hydraulic cylinder of the four-column hydraulic press machine, if there are obstacles, it cannot be enforced.
Are there safety guards on the four-column hydraulic press machine?
On the hydraulic press machine, it is necessary to have safety protection devices, and in terms of the specific types of installation protection devices, there are:
Safety start device: When the operator’s limbs enter the dangerous area, the clutch in the hydraulic press machine will not be closed or the slider will not be able to go down. Only when the operator completely exits the dangerous area, the hydraulic press machine can perform these actions.
Mechanical protection device: When the slider of the hydraulic press machine goes down, separate the dangerous area from the operator’s hands to ensure safe production.
Automatic protection device: light beam, air flow and electric field are set around the dangerous area of the die. Once the operator’s limbs enter the dangerous area, the hydraulic press machine will automatically stop working through the control of radio, electricity and gas to protect the safety of the operator.
Analysis of the causes of gear pump vibration in four-column hydraulic press machine
Analysis of the reasons for the vibration of the gear pump in the four-column hydraulic press machine:
- Whether the gear pump of the four-column hydraulic press machinesucks oil with bubbles from the oil tank.
- Check whether the rubber parts of the four-column hydraulic press machinemotor and pump coupling are damaged or missing. Broken or missing rubber parts of the coupling should be replaced or refitted.
- Check the concentricity of the installation of the four-column hydraulic pump and the motor. There should be a requirement to adjust the concentricity of the installation of the pump to the motor.
- Check the key or spline of the four-column hydraulic press machinecoupling. Wear can cause radial runout of the rotating parts.
Causes of stuck valve in hydraulic press machine system
The reasons for the system stuck valve of the hydraulic press machine are generally as follows: hydraulic clamping caused by unbalanced radial force, unbalanced adsorption of polar molecules in the oil, mixing of impurities in the oil, liquid boundary layer in the gap between the valve core and the valve sleeve. additional resistance and solenoid pushrod deflection on dry solenoid valves.
A slight “hydraulic clamping” increases the frictional resistance when the spool moves, which can seriously cause the system components controlled by the universal hydraulic press machine to lag behind the action and cause the hydraulic equipment to fail. When the hydraulic clamping resistance is greater than the movement force of the spool, the spool will Was “Hydraulically stuck and unable to move. If the movement of the hydraulic spool is driven by electromagnetic force, once the spool is “hydraulically stuck, the AC electromagnet is easily damaged.” Hydraulic clamping will accelerate the wear of the spool valve and reduce the service life of the components.