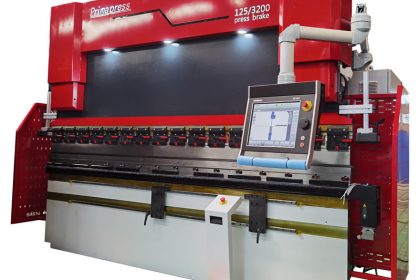
Precautions and usage methods for buying CNC bending machine press brake molds
- How to choose the material of CNC bending machine press brakemold?
How to choose the material of the bending machine press brake mold? Generally use T8 or T10, and the better 42CrMo material, it mainly requires high strength, high toughness and good wear resistance. Choose cold work die steel.
Cr12MoV is a very good material for bending machine press brake moulds, with satisfactory performance and good process performance, the price will be higher. .42CrMo is a high-strength alloy quenched and tempered steel with high strength and good toughness. It can work below 500 degrees.
- The hardness of the bending machine press brakemold
Companies that use bending machine press brake molds may encounter such a problem, that is, the hardness of the bending machine press brake molds in use is not enough to meet the needs of processing materials. When encountering such problems, what should we do? How to solve this kind of problem? The following CNC bending machine press brake mold manufacturers will explain some methods for improving the hardness of bending parts molds for your reference and learning.
1) Correctly select mold steel, and large molds should use high-alloy mold steel with high hardenability.
2) Strengthen the inspection of raw materials to ensure that the raw materials meet the standards. Reasonable forging and spheroidizing annealing treatment of poor raw material steel to ensure a good organization. Carbon tool steel is not easy to be annealed many times to prevent graphitization.
3) Strictly implement the forging process and the spheroidizing annealing process to ensure a good preliminary heat treatment structure.
4) Before heat treatment, the rust spots and oxide scale on the surface of the mold should be removed, and the protection during heating should be paid attention to. Vacuum heating quenching or protective atmosphere heating quenching should be used as much as possible, and good deoxidation treatment should be carried out during salt bath heating.
5) Correctly formulate mold quenching and heating process parameters to ensure sufficient phase change, and perform rapid cooling at a cooling rate greater than the critical cooling rate to obtain a qualified metallographic structure.
6) Correctly select the quenching cooling medium and cooling method, and strictly control the classification and isothermal temperature and time.
7) The moisture content of the alkaline bath should be strictly controlled, the quenching cooling medium used for a long time should be filtered and regularly replaced, and kept clean, and its quenching cooling characteristic curve should be checked regularly.
8) For large-sized molds, properly extend the time of immersion in the quenching cooling medium to prevent the mold from exiting the quenching cooling medium at an excessively high temperature.
3, how to use the bending machine press brake mold correctly
Nowadays, bending machine press brake molds are used in many places, so what exactly is a bending machine press brake mold? How should it be used correctly?
1. Turn on the power of the bending machine press brake, turn the key switch, press the oil pump to start, the bending machine press brake oil pump starts to rotate, and the machine has not yet started to work.
2. The stroke adjustment requires a trial run when the bending work with the bending machine press brake mold is officially started. When the upper die of the bending machine press brake descends to the bottom, there must be a gap of plate thickness. Otherwise it will cause damage to the mold and the machine. The stroke adjustment also has electric quick adjustment and manual fine adjustment.
3. For the selection of the notch of the die of the bending machine press brake, a notch of 8 times the width of the plate thickness is generally selected. If you bend a 4mm sheet, you need to choose a slot of about 32.
4. Check the overlap and firmness of the upper and lower molds of the bending machine press brake; check whether each positioning device meets the requirements of being processed. Frequently check the overlap of the upper and lower molds; whether the instructions of the pressure gauge meet the regulations.
5. The sheet metal must be compacted during bending to prevent the sheet metal from lifting up during bending and injuring the operator.
6. The power supply must be cut off when adjusting the sheet metal die, and the operation should be stopped.
7. When changing the opening of the lower die of the variable bending machine press brake, no material is allowed to contact the lower die.
8. It is forbidden to use bending machine press brake molds to fold over-thick iron plates or quenched steel plates, high-grade alloy steels, square steels, and sheets that exceed the performance of the sheet metal bending machine press brake to avoid damage to the machine tool.
9. Turn off the bending machine press brake, and place wooden blocks on the lower molds under the cylinders on both sides to lower the upper slide plate onto the wooden blocks. Exit the control system program first, then cut off the power supply.
One of the most important goals of CNC bending machine press brake molds in the bending process is to create evenly distributed machining allowances for each type of bending in each bending process. This means that bending molds with different angles must be used, and the main bending machine press brake mold should be as close as possible to the final shape of the mold in each process. The evenly distributed machining allowance of the bending machine press brake mold ensures a constant and high productivity and a safe bending process. When the angle is constant, the bending speed and feed rate can also be kept constant at a high level. In this way, the effect of the mold on the bending machine press brake and the change of the working load are small, so the heat and fatigue generated are also less, thereby increasing the life of the mold of the bending machine press brake.
In order to get the longest life of the bending machine press brake mold, continuous cutting should be kept for as long as possible during the bending process. If the mold of the bending machine press brake enters and exits too frequently, the life of the mold of the bending machine press brake will be significantly shortened. This will increase the thermal stress and thermal fatigue on the cutting edge. There is a uniform and high temperature ratio in the cutting area, and there is a large fluctuation on the mold of modern cemented carbide bending machine press brake