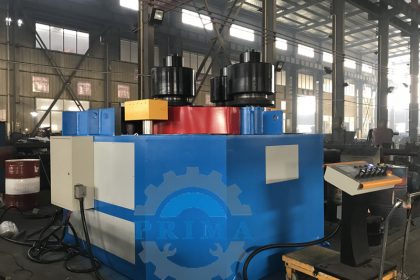
Maintenance part and method of hydraulic CNC tube angle steel profile bending machine
After the failure of the hydraulic CNC tube angle steel profile bending machine, the maintenance personnel should check and eliminate the failure in time, and take the practical life and utilization rate of the targeted electrical equipment to achieve higher economic benefits.
The classification of faults and maintenance measures are as follows
- According to the location of the failure, the period can be divided into software failure and hardware failure
- According to the inevitability of equipment failure of hydraulic CNC profile bending machine, equipment failure can be divided into random failure and systematic failure
- According to the destructiveness of electrical failure of hydraulic CNC profile bending machine, it can be divided into destructive failure and non-destructive failure
- Divided by the operation quality of the hydraulic CNC profile bending machine, with the continuous extension of the service life of the hydraulic CNC profile bending machine, unqualified products may be produced under normal operation. This is due to the movement of the hydraulic CNC profile bending machine. It is caused by the decline of quality and the decline of movement characteristics.
Maintenance and maintenance of electrical systems
- Strictly abide by the mechanical and electrical equipment maintenance management system
- Maintain the input and output devices
- Regularly check whether the electrical system is overheated
- Regular dust removal
- Maintain the accuracy of the electrical equipment of the hydraulic CNC profile bending machine
The occurrence of electrical equipment failure of the hydraulic CNC profile bending machine will not only affect the normal operation of the hydraulic CNC profile bending machine, but also make the operation efficiency of the enterprise low. In severe cases, it will greatly affect personal and machine safety, resulting in Huge human and economic losses.
According to the reasons for the failure of the electrical equipment of the hydraulic CNC profile bending machine, the failure can be basically divided into man-made and natural failures. The natural failure is mainly the insulation aging of the electrical components, the natural wear and tear of the hydraulic CNC profile bending machine parts, and the ambient temperature. It is caused by unavoidable reasons such as the influence of humidity and humidity; the most important personal failure is the machine tool failure caused by unreasonable equipment installation, improper operation or other human damage during the working process of the hydraulic CNC profile bending machine.
How to maintain the hydraulic CNC profile bending machine
Profiles are widely used steel material structures. The standardization, standardization and serialization of profiles not only saves a lot of time, financial and material resources for producers, reduces costs, and achieves good economic benefits, but also facilitates the use of consumers. However, the profiles need to be processed again, such as bending, stamping and other processes before they can be put into production. During the secondary molding, it is necessary to design and use professional equipment to ensure the molding quality. The commonly used forming process is bending forming.
The hydraulic CNC profile bending machine is a high-efficiency processing equipment specially used for bending angle steel, channel steel, I-beam, flat steel, square steel, round steel and other special-shaped steel.
The main points to be paid attention to in the bending operation of the hydraulic CNC profile bending machine are as follows:
- First, fix the upper die so that the center of gravity of the die and the center of the pressure head are in a straight line; the planes of the upper and lower die must be in close fit, with a uniform gap, and check that the upper die has enough stroke.
- Start the hydraulic CNC profile bending machine, test the pressure, check whether there is any abnormality, and whether the lubrication is good. For workpieces that are difficult to remove from the mold, add some lubricant or lubricating oil appropriately to reduce friction for easy mold release.
- Before the formal bending, it is necessary to check again whether the workpiece number and size are consistent with the drawings, and whether the blank has burrs that affect the pressing quality. For workpieces with large batches, a block that can adjust the positioning must be installed, and the position of the block should be adjusted in time if the deviation is found.
- It is forbidden to pick and place the workpiece directly on the mold of the hydraulic CNC profile bending machine by hand. For larger workpieces, pick and place outside the mold. For workpieces smaller than the mold, other tools should be used to pick and place.