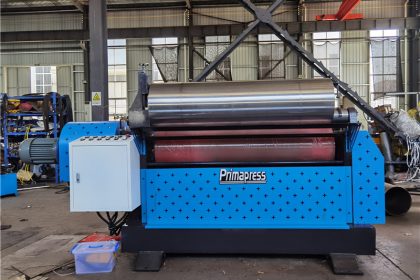
Main features and precautions for use of the two-roll plate rolling machine 2 rolls bending machine
The two-roll plate bending machine is a metal plate bending and correction machine, which is specially used for the forming and bending of metal plates. The four-roll plate rolling machine can complete the pre-bending and crimping of various specifications of cylindrical and arc-shaped workpieces after one-time feeding. With the help of auxiliary devices, the conical cylinder can be rolled.
The two-roll plate bending machine has two rollers, the upper roller is the active roller, the lower roller can move up and down to clamp the steel plate, and the two side rollers can be lifted and lowered along the oblique line. Bending work, it depends on the rise of the lower roller to press the end of the steel plate between the upper and lower rollers. The movement of the re-use side rollers bends and deforms the end of the steel plate to achieve the required style.
The two-roll plate bending machine is used to bend metal plates of a certain thickness into cylindrical, arc or tapered parts at normal temperature. Its characteristics are as follows:
- One-time feeding, the rolling can be completed without turning around;
- The three working rolls of the machine are all main drive rolls, which prevents slippage when rolling and expands the rolling range of steel plates;
- The lifting and lowering of the upper roller and the translation of the lower roller are hydraulically driven;
- Microcomputer control, automatic leveling, LCD display;
- The machine integrates machinery, electricity and hydraulics, and each action is interlocked to protect each other;
Safety matters needing attention in the operation of the two-roll rolling machine
Two-roll plate bending machine is a general-purpose equipment for bending metal sheet into cylindrical, arc or other shaped workpieces. The plate roller press with two rollers upper roller drives the roller, the lower roller and the side roller are driven, the upper roller is fixed, the lower and side pulleys can be lifted and moved, the upper roller is driven by a hydraulic motor, the rotation of the lower and side rollers is made by Friction between the steel plate and each roll. The lower roller and the side roller are driven by the oil cylinders at both ends to realize the lifting movement. The turning and resetting of the front bearing seat of the upper roller is completed by the inverted oil cylinder. The bearing seat and oil cylinder of each roller are installed on the frame at the left and right ends. The left and right frames are the main body of the four-high rolling mill, which is welded and installed on the overall base. The push-roll unit is used to roll the finished part. After turning the inverted cylinder into place, push the workpiece out of the machine. All operations of the machine are carried out on the stage.
Precautions for the safe operation of the two-roll rolling machine are as follows:
- The operator should understand the structure and performance of the machine, be familiar with the operation method of the control system and the bending process of the workpiece, and strictly abide by the operation matters.
- All buttons of the electronic control system must be in their original positions before starting and stopping.
3: During use, the oil supply of each lubrication point and reducer should be checked frequently to maintain the specified oil level.
4: During operation, if there is irregular noise, impact and swing, it should be stopped in time for maintenance.
5: During use, always check the transmission mechanism and connecting parts, do not loose, do not damage.
6: The steel plate is not allowed to roll directly on the machine, unevenly welded or flattened.
7: When the plate enters the formal bending, it must be perpendicular to the center line of the idler.
8: During the bending process, the sheet must move with the rollers, no slippage is allowed.
9: When the tapered workpiece is bent and wound, the small end of the tapered must be at one end of the overturned bearing.
10: During the winding process, the upper roller can be lifted and lowered only when the drive is stopped, the overturning bearing is removed, and the upper shaft is lifted.
11: The work of unloading is that after the machine stops, first loosen the overturning bearing, then take it down, flatten it, press the cancel button on the upper roller, make one end of the upper roller (3 degrees), take out the workpiece, and press the lower button on the upper roller to make the upper roller. Roll flat, close overturn bearing, and complete a work cycle.