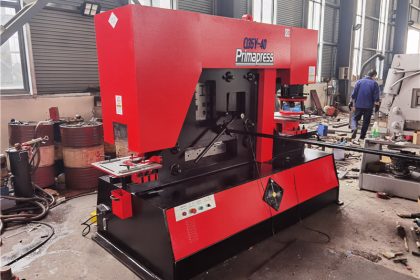
How to prolong the service life of hydraulic ironworker combined punching and shearing machine parts?
The hydraulic ironworker combined punching and shearing machine is a kind of machine tool equipment that integrates multiple functions such as metal shearing, punching, shearing, bending, etc. It has the advantages of simple operation, low energy consumption, low maintenance cost, etc. It is the preferred equipment for metal processing in modern manufacturing industry (such as metallurgy, bridge, communication, power, military industry, etc.).
- Punch bar
The punch, like a piston, transfers the energy of the equipment to the punch. The alignment and installation of punches is critical, especially for some old or frequently used press equipment.
Generally, the punch is harder than the punch. This may eventually lead to wear of the contact point between the punch bar and the top of the punch. If this happens, the punch will make the uneven punch surface vibrate violently.
To deal with this situation, you can quickly check whether this problem exists by using a square and straight object edge. Most punch bars of the hydraulic ironworker combined punching and shearing machine are connected with the upper part of the stamping parts by bolts. During the operation, the bolts may become loose, so they should be checked frequently and reinforced according to the instructions.
Other punching and shearing machine punches are equipped with punch alignment locators, such as single groove, cross groove, vertical groove, or “V” shaped cross groove. When using a punch equipped with a positioner of the same shape, the positioner can effectively prevent the punch from rotating. Especially when punching square, oval and rectangle holes, the positioner can be quickly assembled, which is particularly practical. In addition, they can help technicians to ensure that the molds used are aligned.
- Die fixing
The correct alignment of the die holder and die holder is as important as the punch. The die holder of the combined press and shear is used to connect and fix the die and the press equipment and ensure that it is in the center position under the punch. Some combination presses are equipped with removable die holders or die inserts. These are the easily worn parts of the fixed parts of the hydraulic ironworker combined punching and shearing machine.
How to prolong the service life of hydraulic ironworker combined punching and shearing machine parts?
The punch transfers most of the energy from the die of the hydraulic ironworker combined punching and shearing machine to the die as a fixed part. The die is usually harder than the die holder. This may cause wear at the contact point (die bottom) between the bottom of the die and the bottom of the die holder. Finally, a damaged die holder may cause the die to not be properly inserted and fixed.
In this case, the inner diameter of the die holder begins to wear into oval shaped holes, which further aggravates the problem of misalignments. When the wear degree of the die seat exceeds the acceptable range, the die seat or the whole die fastener needs to be replaced.
Bolts or other die fixing parts used to fix the hydraulic ironworker combined punching and shearing machine and the installation parts of the punching and shearing machine equipment shall be checked and reinforced from time to time.
Machine vibration, tensile load and other conditions may cause parts to loosen.
Die fixings can usually be aligned and positioned by fixing screws or pin slots. When using a die equipped with the same device, these devices can stabilize the die to ensure that it does not rotate during processing.
The die should have a suitable notch, flat surface, pin, etc., especially when using a forming punch equipped with a positioning device. These small investments in adding positioning devices to tools can avoid unnecessary tool damage and bring long-term benefits.
- Stripper
The tool life is also affected by the stripper. When a punch is completed, the stripper allows the press equipment to withdraw the punch from the sheet. If the stripper is not used correctly, the punch may be damaged by punching only a few holes.
If the bottom of the stripper is not parallel, warped or uneven with the punched sheet, or the punched sheet is warped, the sheet will be wedged into the punch.
When the punch is pulled out of the sheet by the punching machine, the lateral force brought by the sheet wedged into the punch will cause the punch to peel off. In extreme cases, the punch may even break.
Some strippers can be connected to the punch and in contact with the sheet. Others need manual adjustment. When using a manual stripper, the space between the bottom of the stripper and the top of the sheet should be adjusted to a minimum.
- Lubricant
It is important to add lubricant to the tools on the press equipment to prolong the service life of the tools. Understanding the force in the small space between the punch and the machined plate may help to understand the importance of lubricants.
When the punch passes through the sheet, a small part of the metal on the sheet will melt on the punch surface. As the punch processing continues, the melt will accumulate more and more in the punch, which will cause the actual diameter of the punch to become larger.
This will lead to a vicious circle. Because the gap between the punch and the die becomes smaller and smaller, the punch will eventually press on the die.
The lubricant can form a protective film between the punch and the plate. The utility model can effectively reduce the metal melt on the punch, thereby prolonging the service life.
From the early use of pig fat as a lubricant, to the use of synthetic lubricants, to the advent of modern lubricants. The most frequently asked question is: Which lubricant is the best?
Obviously, the higher the viscosity of the lubricant, the stronger the protection. In particular, the lubricant with higher viscosity has a remarkable effect on the slow impact punch However, in the rapid stamping equipment, the protective film at the edge of the punch may form a viscous vacuum film to isolate air.
When the punch of the hydraulic ironworker combined punching and shearing machine retracts rapidly, the metal block punched last time may remain in the die, which will make the new metal block attach to the surface of the punch. Obviously, if the press equipment continues to operate, the tools will be seriously damaged. The lubricant is too thin to provide effective protection for the tools used for processing thick plates, but the amount is just right for processing thin plates.