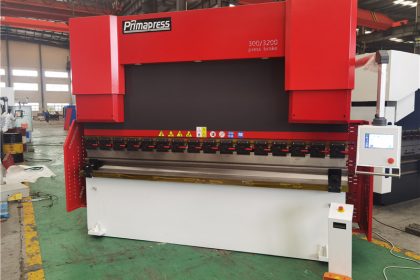
Common faults and angle problems of hydraulic sheet metal bending machine press brake
What should I do if the angles folded on both sides of the torsion axis CNC bending machine press brake are inconsistent?
The application of the numerical control system on the torsion axis numerical control bending machine press brake can not only improve its performance, but also make it have the advantages of compact structure, easy operation and high reliability. Carry out high-precision positioning control; with one-way or two-way positioning function, which can effectively eliminate the lead screw transmission gap and improve positioning accuracy; the position of the back gauge and the slider has the function of automatic parameter search and automatic memory of the actual position after power failure; with single-step , Multi-step programming function, can realize automatic operation after setting.
Equipped with the function of retreating and escaping materials to avoid the interference between the back gauge device and the bending workpiece; the solenoid valve can quickly configure the working conditions of the solenoid valve in the states of slider quick-down, work-in, unloading and return; the system has intuitive hardware diagnosis Monitoring makes the machine tool more convenient to maintain and use; it adopts simple parameter programming and has complete detection, and the system detects the input data and prompts for correction; it provides the function of analog upper limit, and there is no need to return to the upper limit after processing is completed. Improve processing efficiency.
Are the angles folded on both sides of the torsion axis CNC bending machine press brake inconsistent?
Reason: The two sides have different heights.
Adjustment: 1. Put a plate of the same thickness on both sides, fold the workpiece more than 90 degrees, and measure the angle with an angle ruler.
- The connecting rod connecting the two worm gear seats on the bending machine press brakeis disengaged. Just pull it to one side. There are springs inside to prevent it from falling out.
- Compare the two board angles. If the right angle is large, turn the right link clockwise. After turning a certain position, the folding plate is measured.
- Repeat the third step until the angles on both sides are the same. Install the connecting rod.
- After installing the connecting rod, try folding again at a different angle. See if the angle is the same. If the angle is still inconsistent, check whether the synchronization mechanism is damaged, such as slippage at the connecting rod connection and damage to the worm gear.
The torsion axis CNC bending machine press brake is prohibited from folding super-thick iron plates or quenched steel plates, high-grade alloy steel, square steel and plates that exceed the performance of the plate bending machine press brake, so as not to damage the machine tool, and no welding scars and Large burr to prevent mold damage. All parts of the machine tool should be kept lubricated regularly, the operator should add lubricating oil once in each shift, and the equipment must be overhauled and maintained once every six months. After the work is completed, the oil pump should be turned off, the power supply should be cut off, and the machine tool and the environment should be cleaned.
Analysis and elimination of common faults of hydraulic sheet metal bending machine press brake
The working process of the hydraulic sheet metal bending machine press brake generally includes several beats of fast down, slow down, work advance and return. The danger occurs in the down stage of the tool, and the dangerous area is below the tip of the tool. The floating safety light curtain can form a protection area under the tool tip and move synchronously with the tool to ensure that any object must enter the protection area of the light curtain before touching the tool tip when the tool goes down. The floating safety light curtain control system According to the working process of the bending machine press brake, a signal can be sent to the bending machine press brake system to interrupt the slide down and monitor the status of the safety double valve.
Analysis and elimination of common faults of hydraulic sheet metal bending machine press brake:
The sliding block slides down; the hydraulic sheet metal bending machine press brake often has a sliding block sliding fault during use. From its principle analysis, the sliding block is connected to two hydraulic cylinders. The reason for the sliding block sliding is that the hydraulic cylinder cannot be locked according to the principle analysis. . There are two main reasons why the hydraulic cylinder is not locked, one is the internal leakage of the hydraulic cylinder, and the other is the failure of the hydraulic control check valve.
Fault analysis:
Analysis 1: When there is internal leakage in the hydraulic cylinder, the pressure oil in the rod cavity leaks into the rodless cavity, and the hydraulic cylinder slides down, which drives the slider to slide down, and the positioning and locking function required by the bending machine press brake cannot be achieved. The common cause of internal leakage in hydraulic cylinders is the damage or aging of the seals, and it may also be that the piston rod and the cylinder block are too worn; if the cause of the failure is the damage or aging of the sealing ring, choose to replace the sealing ring directly. If the cause of the failure is the excessive wear of the piston rod and the cylinder block, it can be repaired by electroplating or metal brushing, which is costly.
Analysis 2: When the hydraulic control check valve fails, that is, the locking function of the hydraulic control check valve fails. When there is no high-pressure oil passing through the control oil port, the oil direction of the hydraulic control check valve is reversed. When it is determined that the hydraulic control check valve is faulty, disassemble the hydraulic control check valve to check the fault, or choose to replace the hydraulic control check valve directly.
Troubleshooting: According to the above analysis, using a portable tester to test, the hydraulic control check valve locking function is normal. After testing the hydraulic cylinder, it was found that there was serious internal leakage in the left hydraulic cylinder. The end cover of the left hydraulic cylinder was removed, and it was found that the sealing ring was severely worn and deformed.