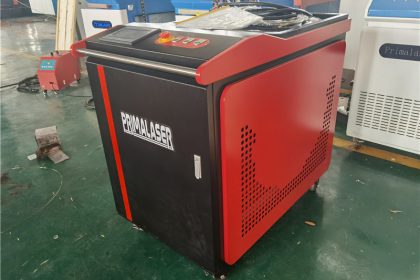
Application of fiber laser welding machine fiber laser welding in kitchenware industry
In recent years, fiber laser welding has become more and more widely used as a new welding method, especially after the price of lasers has been greatly reduced, the application of fiber laser welding in some fields such as blowout explosion. Kitchen utensils have always been a necessity in our lives. With the continuous improvement of people’s living standards, daily kitchen utensils must also continuously meet the aesthetic and personalized needs of customers. In short, the classification of kitchen utensils is generally composed of stainless steel kitchen utensils, iron kitchen utensils, ceramic kitchen utensils, plastic kitchen utensils, etc. As far as the welding process of stainless steel kitchen utensils is concerned, the traditional welding technology is difficult to achieve the desired effect, and the post-weld treatment The workload is large, and the emergence and promotion of fiber laser welding technology has broken this deadlock and made a significant breakthrough in the welding process of kitchen utensils.
Principle of fiber laser welding
As a high-quality, high-precision, low-distortion and high-efficiency welding method, fiber laser welding is widely used in machinery manufacturing, aerospace, automotive industry, powder metallurgy, biomedicine, etc., especially in the kitchenware industry represented by stainless steel kitchenware The application is more extensive.
fiber laser welding is to radiate a laser beam with high energy density to the metal surface. Under the interaction between the laser and the metal, the metal absorbs the laser energy and converts it into heat energy. After the metal is melted, it cools and crystallizes to form a weld. fiber laser welding has the advantages of fast welding speed, small workpiece deformation, large weld fusion, good weld quality, and simple post-weld processing. It can be used to weld the same or dissimilar materials or refractory materials in various environments. The schematic diagram of fiber laser welding is shown in Figure 1.
In the processing of stainless steel kitchen utensils, in order to achieve better welding results, more and more kitchen utensils companies use fiber laser welding technology. After welding, the deformation of the workpiece is small, and the subsequent processing workload is small, which can obtain a very beautiful welding surface effect, and can greatly reduce the labor cost of polishing and leveling processes.
fiber laser welding equipment commonly used in the kitchenware industry
The most commonly used fiber laser welding equipment in the kitchenware industry is generally divided into three types: double-station robot fiber laser welding unit, fiber laser welding machine and hand-held fiber laser welding machine.
Double station robot fiber laser welding cell
The dual-station robot fiber laser welding unit is shown in Figure 2. It consists of a robot, a dual-station rotary positioner, a laser, and a protective room. The manual feeding method is used to realize internal welding and external loading and unloading, and improve the efficiency of equipment use. and production efficiency. Usually, the rotary positioner is equipped with adjustable fixtures to meet the welding of workpieces of different specifications, and has strong versatility. This welding unit is mainly suitable for the welding of medium and large kitchen utensils with many long welds.
fiber laser welding machine
As shown in Figure 3, the fiber laser welding machine is mainly composed of X, Y, Z three axes and rotating axes, laser, closed cover, etc. The welding of workpieces is realized by manual loading and unloading. This special welding machine is mainly suitable for the welding of small kitchen utensils with a single welding seam. The rotating shaft is equipped with different fixture systems to adapt to a variety of workpieces, with high flexibility.
Handheld fiber laser welding Machine
The hand-held fiber laser welding machine is shown in Figure 4. It is mainly composed of a laser, a water cooler, a hand-held welding head, etc. It occupies a small area, is quick to use, and has low requirements for operators. The initial cost investment is less, and the grinding workload after welding of stainless steel kitchen utensils can be greatly reduced. Therefore, hand-held welding machines are currently the first choice for small kitchen utensil manufacturers.
Design Ideas of Fixtures for fiber laser welding of Typical Workpieces
The use of fiber laser welding in the kitchenware industry has become a development trend. Some domestic manufacturers have applied fiber laser welding to the welding of hardware kitchenware, especially the welding of the covers of large kitchenware such as range hoods and ovens, which has greatly improved production efficiency. good welding effect. The following takes the fiber laser welding of the range hood hood as an example to briefly analyze the design ideas of the fixture.
The model and real object of the range hood are shown in Figure 5. The range hood is generally cut and stamped by laser cutting, and the consistency of the workpiece is kept well. The design ideas of fixtures for such workpieces are generally as follows:
(1) First determine the position of the workpiece, and find the positioning datum according to the requirements of the drawing. Since the hood is very loose after stamping and forming, the side edge cannot be used for positioning, and the positioning method of hole + large surface is generally adopted.
(2) Determine the number of welds and whether the welding is convenient. In the case of ensuring the size of the workpiece, the welding of long seams is given priority. If the short seam affects the fixture design, resulting in high cost, it is necessary to communicate with the customer whether follow-up repair welding can be adopted in combination with the cost.
(3) Determine the form of welding fixtures. Determine the degree of automation of the fixture according to customer needs, whether to use manual clamping, automatic clamping, or a combination of manual clamping and automatic clamping.
⑷ Ensure that the fixtures are easy to adjust. In order to ensure the convenient adjustment of the designed tooling positioning block and clamping block, the form of adjustment shims or waist hole adjustment, pin positioning, etc. can be used to reduce the amount of rework of the tooling and fixture parts.
The manual clamping tool for the cooker hood that has been normally used at the customer’s site is shown in Figure 6. Due to the increase in customer output, according to the customer’s needs, the pneumatic clamping tool is redesigned to improve work efficiency, as shown in Figure 7 .