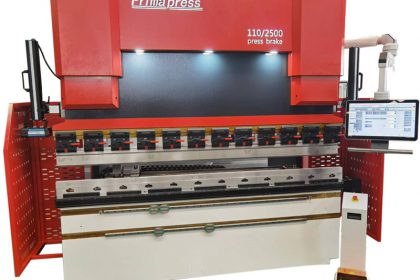
Introduction to professional terms in sheet metal processing industry of CNC bending machine
Every industry has its own terminology, and the CNC bending machine sheet metal processing industry is no exception. The following 25 are common.
(1) Riveting: refers to the process of firmly pressing rivet nuts, rivet screws, rivet nut columns and other fasteners onto the workpiece with a punch or hydraulic press.
(2) Riveting: refers to the process of sinking the workpiece first, and then firmly pressing the rivet nut on the workpiece with a punch or hydraulic press.
(3) Pulling nut: refers to the process similar to riveting. The process of firmly connecting the rivet nut (POP) and other connecting pieces to the workpiece with a master gun.
(4) Riveting: refers to the process of closely connecting two or more workpieces with a rivet gun as a tool.
(5) Riveting: the process of connecting two or more workpieces face to face with rivets. In case of countersunk riveting, the workpieces shall be countersunk first.
(6) Corner cutting: refers to the process of cutting the workpiece corner with a die on a punch or hydraulic press.
(7) Bending: refers to the process in which the workpiece is formed by a bending machine.
(8) Forming: refers to the process of using a die to deform a workpiece on an ordinary punch or other equipment.
(9) Material cutting: refers to the process of obtaining rectangular workpiece from materials through plate shearing machine.
(10) Blanking: refers to the process of workpiece cutting by LASER or blanking by CNC punch.
(11) Blanking: refers to the technological process of using a die to process the product shape on an ordinary punch or other equipment.
(12) Punching: refers to the process in which the workpiece is processed by an ordinary punch and die.
(13) Punching bump: refers to the process of forming a convex shape of the workpiece with a die on a punch or hydraulic press.
(14) Punching and tearing: also called “punching bridge”, it refers to the process of forming the workpiece into a bridge like shape with a die on a punch or hydraulic press.
(15) Hole drawing: also called “flanging”, it refers to the process of using a die to form a round hole on the workpiece on an ordinary punch or other equipment. Process.
(16) Tapping: refers to the process of machining internal threads on the workpiece.
(17) Leveling: refers to the process of using other equipment to level the workpieces that are not smooth before and after processing.
(18) Tooth retraction: refers to the process of repairing the second screw tooth of the workpiece with pre tapped teeth.
(19) Drilling: refers to the process of drilling the workpiece with a drill on a drilling or milling machine.
(20) Chamfer: refers to the process of processing sharp corners of workpieces with molds, files, grinders, etc.
(21) Stamping: refers to the process of stamping words, symbols or other marks on the workpiece with a mold.
(22) Counterbore: refers to the technological process of machining tapered holes on the workpiece to fit with connectors such as countersunk screws.
(23) Flattening: refers to the process of transition from a workpiece with a certain shape to a flat workpiece.
(24) Punching mesh hole: refers to the mesh hole punched on the workpiece with a mold on an ordinary punch or a CNC punch.
(25) Reaming: refers to the process of turning small holes on the workpiece into large holes with a drill or milling cutter.
- The number of stamping operations is simple and convenient, which has advantages for workpieces with complex shapes, but the thickness should be within the range of machinability. After the program is completed, the circuit board can be processed automatically. In addition to the need to invest a certain cost in the early stage, the low investment cost in the later stage can help enterprises improve economic efficiency.
- Quality of finished products. The quality of stamping parts is very good, which not only has high precision and flatness, but also makes the products consistent.
- CNC punching machine has high production efficiency. The digital punch can realize the batch production of parts, and the production speed is fast. NC bending machine sheet metal processing not only has high speed and good quality, but also has a variety of processing methods, such as single punch, continuous punch and array punch.