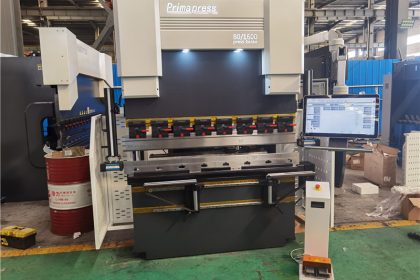
Advantages of Electro hydraulic Servo Synchronous cnc press brake bending machine
Electro hydraulic servo synchronous Ccnc press brake bending machine is suitable for large steel structures, iron towers, street lamp posts, high lamp posts, automobile girders, automobile cargo boxes and other related industries. Its essence is a numerical control bending die for bending thin plates. The die is composed of a bracket, a workbench and a clamping plate. The coil is energized to generate gravity on the pressing plate, thus completing the clamping of thin plates between the pressing plate and the base. Because the method of electromagnetic force clamping is adopted, the pressing plate is made according to specific workpiece requirements, which is simple to operate and can process workpieces with side walls.
The electro-hydraulic servo synchronous Ccnc press brake bending machine is developed according to the principle of plastic plate heating and softening and melting welding. It is suitable for all thermoplastic materials. The bending machine mold has the following characteristics: direct bending, no splicing, no slotting, no welding rod required, its corner corner appearance is beautiful without water leakage, at the same time, the processing speed is fast, the corner corner treatment surface is beautiful, and the strength is high. It transforms manual welding into fully automatic machine operation, improves quality, improves labor efficiency, reduces labor costs, and greatly shortens the production cycle of products.
Advantages of electro-hydraulic servo synchronous Ccnc press brake bending machine:
- Direct angle programming with angle compensation function.
- The grating ruler real-time detection feedback correction, full closed loop control, rear stopper and slider dead stopper positioning accuracy is ± 0.02mm.
- The upper die adopts a quick clamping device, and the lower die adopts a wedge deformation compensation mechanism.
- With multi step programming function, it can realize multi automatic operation, complete one-time processing of multi step parts, and improve production efficiency.
- The imported hydraulic system with stable performance and compact structure can be selected according to user requirements, and the ball screw and synchronous belt drive can be selected for the rear stopper.
Sheet metal processing can process parts with complex shapes
As the sheet metal parts mainly use the stamping processing technology, and the stamping processing is to use the pressure provided by the stamping equipment to make the metal sheet plastic deformation through the stamping die, and produce the required processing method of parts with a certain shape and size, the sheet metal processing tools have the following characteristics.
(1) Parts with complex shapes can be processed, and the waste generated in the production process is less.
(2) The product has sufficient shape and dimension accuracy, good interchangeability and good surface quality.
(3) Parts with light weight, low material consumption and high strength and stiffness can be obtained.
(4) Processing mostly depends on special molds, and mold manufacturing is complex and costly. Therefore, only under the condition of mass production can the cost of parts produced be significantly reduced.
And because the assembly and connection of sheet metal parts mainly uses welding processing technology, and welding processing is a processing method that uses heat energy or pressure, or both, and uses or does not use filler materials to achieve permanent connection by using the combination between the atoms of two objects. Therefore, sheet metal processing has the following characteristics.
(1) Compared with the production and processing of forgings and castings, sheet metal components have the advantages of light weight, saving metal materials, simple processing technology, reducing production costs, and saving production costs.
(2) Most of the sheet metal components processed by welding have low processing accuracy and large welding deformation, so the amount of deformation and correction after welding is large.
(3) Parts with light weight, low material consumption and high strength and stiffness can be obtained.
(4) Processing mostly depends on special molds, and mold manufacturing is complex and costly. Therefore, only under the condition of mass production can the cost of parts produced be significantly reduced.