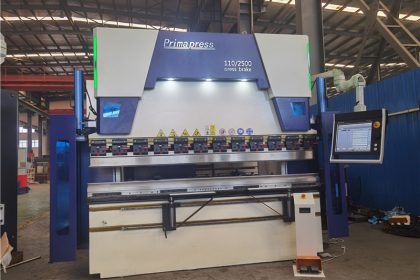
Advantages and problems of the slide block of the NC hydraulic press brake bending machine
The manufacturability of bending parts refers to the adaptability of bending parts to stamping process. Generally, when formulating the stamping process plan, the manufacturers of the four roll plate hydraulic press brake bending machine must consider the processability of the bending parts. As roll bending is a form of stamping process, it is necessary to briefly analyze several technological indexes related to sheet metal bending in this paper.
1、 Bending accuracy
The accuracy of bending parts mainly refers to the accuracy and stability of its shape and size. It is related to the mechanical properties and thickness of the sheet metal, the structure and accuracy of the forming tools, the number and sequence of processes, the shape and size of the workpiece itself and other factors. For the rolled plate, it is generally necessary to consider whether the roundness, cylindricity, unfitness, unfitness and other indicators of the formed cylinder section are within the design requirements.
2、 Minimum bending radius
When the relative bending radius r/t of the bending piece is small to a certain extent, the tensile strain of the fiber on the outer surface of the bending piece will exceed the allowable limit and crack or fracture will occur, so there is a minimum bending radius limit for the bending piece. On the premise that the fiber on the outer surface of the plate will not be damaged, the minimum radius of the inner surface that the workpiece can bend into is called the minimum bending radius rmin, and correspondingly, rmin/t is called the minimum relative bending radius. The factors that affect the minimum bending radius usually include the mechanical properties of the material, the relationship between the fiber direction of the material and the direction of the bending line, the surface quality and section quality of the sheet, the width of the bent sheet, the thickness of the sheet, etc.
When using the hydraulic press brake bending machine for material operation, you should master the machine and equipment parameters skillfully. During the setting process, you should pay attention to setting the machining allowance parameters of the equipment, and then process the materials according to the requirements. Only in this way can you ensure that the allowance parameters in the processing process meet the requirements, and not only can you improve the working efficiency of the equipment. It can also prolong the service life of the machine.
Advantages of products processed by CNC hydraulic press brake bending machine:
As we all know, CNC hydraulic press brake bending machines are widely used now. Why do so many manufacturers choose CNC hydraulic press brake bending machines for processing?
- Good flexibility
The CNC hydraulic press brake bending machine is flexible after processing, without cutting tools and molds. Combined with CAD/CAM technology, it can cut plates of any shape and size, especially suitable for cutting parts of many varieties, small batches and complex shapes.
- High processing efficiency
Bending and cutting are non-contact processing. There is no impact force during mechanical blanking. There is no wear of tools and molds. There is no need for mechanical blanking. Workpieces are closely arranged, which can save 20% – 30% of materials. Cutting can be formed at one time without subsequent processing.
- High precision
Wuxi Shenchong bending and cutting incision is narrow and smooth, without round corners and rough edges often found in mechanical blanking; The heat affected zone, thermal stress and thermal deformation are small.
What is the reason for the long pause time of NC hydraulic press brake bending machine slider conversion?
- Air is sucked into the upper chamber of the oil cylinder, and the pressure is established for a long time.
- The flow of liquid filling valve or self-priming pipeline is small, or the sliding block moves down too fast, causing vacuum suction.
- The charging valve is not completely closed, and the pressure in the upper chamber decreases slowly.
- When the slow down valve is powered on, close the charging valve, and the upper chamber cannot absorb oil.
- The wrong center position of the proportional valve leads to different openings and asynchronous operation.
- Whether there is a pause in the test of reducing the fast downward speed.
- The fast downforce has an impact on the closing of the charging valve, so the fast downforce can be eliminated.
- Adjustment of pressure parameters in the delay stage before work.
- The damping hole of the control pipeline of the charging valve is too small, forming a differential pressure.
- NC system parameters, delay before slow down.
- CNC system parameters and slow down gain parameters are reduced.
The finishing allowance of the hydraulic press brake bending machine shall be determined through analysis and calculation. For various factors affecting the finishing allowance, the calculation formula and certain test materials shall be used for comprehensive analysis and calculation to determine the finishing allowance. The finishing allowance determined by this method is more economical and reasonable, but there must be relatively complete and reliable test data.