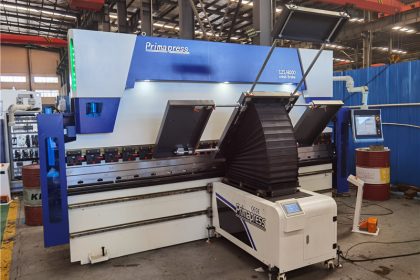
Instructions for programming steps of electro-hydraulic servo synchronous cnc press brake bending machine
The electro-hydraulic servo synchronous cnc press brake bending machine is widely used, and gradually replaced the ordinary bending machine. The CNC sheet metal bending machine is controlled by the digital control system and adopts a certain shape of the mold, so that the sheet is bent and deformed by force and accurately folded. Bend to fit parts to meet machining requirements.
On the machine tool, the movement of the machine tool includes the front and rear movement X of the back gauge, the up and down movement of the slider Y, the left and right movement of the stopper Z, and the up and down movement of the stopper R, etc. (see the figure below). The number of control axes of the machine tool is generally combined with X axis, Y1, Y2 axis, R axis, Z1, Z2 axis.
1 Enter part parameters
Sheet thickness, material, length, inner and outer dimensions
2 Determine the part size
After confirming the general part parameters, enter the graphics input interface. When drawing the shape of the part, first enter a basic length value of the part, then enter the angle and length of the adjacent sides, and repeat this process until the part is drawn.
3 To realize the automatic bending step, the following parameters need to be determined:
- The best degree
The optimal degree reflects the calculation precision selected by the system, and the degree selection range is 1-5.
- Front expansion ratio
The forward expansion ratio is the ratio of the length that the material is allowed to extend forward after being compressed. max=1.0.
- Pre-receive expansion factor
Selecting a programming mode of 0 means that when the system calculates no result according to the selected pre-expansion ratio, it will receive a value smaller than the selected value; selecting a programming mode of 1, the system will always execute the selected pre-expansion ratio, This may lead to incomprehensible results.
- Back gauge function
Rear stopper sharp corner positioning: When the back stopper part of the bent sheet is positioned at a sharp angle less than 90 degrees, you can choose whether to allow the rear stopper to realize the material stopper. Select “0” to disallow; select “1” to allow. There is a bend between the stopper and the lower die. Tolerance of angle in horizontal direction: When there is a horizontal angle difference in the rear stopper, the tolerance of the angle can be input for the system to calculate the stopper position of the rear stopper. Vertical Angle Tolerance: When there is a vertical angle difference in the back gauge part, you can input the angle tolerance for the system to calculate the position of the back stop. The length of the blank of the stopper part: the length of the blank of the stopper part refers to the length of the blank from the center of the mold to the back stopper. Due to the limitation of the position adjustment of the X-axis and R-axis, the minimum and maximum lengths of the sheet length of the stopper part are fixed. Within this size range, the sheet can be reliably stopped by the stopper.
- Expand the length calculation
After preprocessing the above parameters, the system can calculate the unfolded length of the sheet and the basic conditions of bending.
How to use the electro-hydraulic servo synchronous cnc press brake bending machine after installation and debugging:
- Power on.
- Install the upper and lower molds.
- Enter the mold library according to the actual size.
- Programming procedures.
- Trial folding workpiece.
- Works normally.
The points that need to be paid attention to when using the electro-hydraulic servo synchronous cnc press brake bending machine are:
- In the case of a new machine, first check the parallelism of the slider and debug it to the standard used.
- The parallelism of the back gauge fingers. Generally, a bending machine within 3.2 meters has 2 fingers, and the front end of the fingers should be kept on a plane.
- The main motor keeps rotating forward. If it is reversed, the hydraulic oil pump has no output.
- The guardrail is closed in place, and people cannot stand at the rear stopper. Pay attention to personal safety.
5, the boot can find the reference point.
- When entering the mold library, pay attention to the correct entry of parameters, otherwise the bending angle will be inaccurate.
- When programming, pay attention to modify the material, thickness and length first; the upper and lower molds are selected correctly.