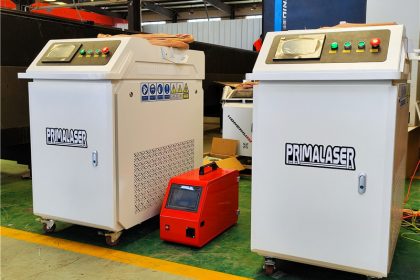
How to extend the service life of metal plate fiber laser welding cleaning and cutting machine
The laser welding equipment uses the pulsed laser with a wavelength of 1080nm generated by the laser to radiate the surface of the workpiece after beam expansion, reflection and focusing. The surface heat diffuses to the interior through heat conduction, and the width, energy, peak power and repetition of the laser pulse are precisely controlled by digitalization. The frequency and other parameters can melt the workpiece and form a specific molten pool, so as to realize the laser welding of the workpiece and complete the precision welding that cannot be achieved by the traditional process.
Laser welding is mainly aimed at the welding of thin-walled materials and precision parts, and can realize spot welding, butt welding, stitch welding, sealing welding, etc., with high aspect ratio, small weld width, small heat affected zone, small deformation, and fast welding speed. The welding seam is smooth and beautiful, and no treatment is required after welding. It can be precisely controlled, the focusing spot is small, the positioning accuracy is high, and it is easy to realize automation.
So, what problems should be paid attention to in the use of metal plate fiber laser welding cleaning and cutting machines?
Today, Prima Laser will talk to you about the matters needing attention in the operation of the metal plate fiber laser welding cleaning and cutting machine. Sincerely hope to be helpful to everyone.
- The appearance of the equipment host and welding head should be dustproof.
- Do not stack debris on both sides of the water machine and keep a space of 1 meter to ensure ventilation and cooling.
- Check the welding head protection lens in the morning shift every day, and then turn on the gas. (During inspection, the protective mirror drawer can be pulled out halfway to see the middle of the lens)
- If the energy is weakened during the welding process, stop the machine immediately and check the protective lens. The inspection method is the same as above. If there is black burn, replace it in time.
- Precautions when replacing protective lenses:
①Turn off all blowing and blowing equipment near the welding head first. Reduce air movement.
② Wipe the periphery of the protective mirror drawer with a clean cloth dipped in alcohol or acetone.
③After removing the protective mirror drawer, immediately seal the protective mirror drawer window with textured paper to prevent dust from entering the welding head.
④When replacing the protective lens, you should pinch the side of the lens if you cannot touch the surface of the lens.
⑤After changing the lens, use a blower to blow off the dust on the surface.
⑥Remove the masking paper, and put the protective mirror drawer back in the correct direction.
- Welding should minimize welding fumes. If there is too much fumes, a dust extraction device should be equipped to remove the fumes.