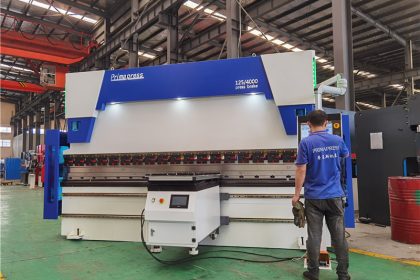
Structure and maintenance method of metal sheet CNC hydraulic press brake bending machine
In view of the maturity of PLC control technology, it is very practical to design a hydraulic sheet metal bending system controlled by PLC. This PLC-controlled system has changed the shortcomings of the traditional manual operation, not only improved the accuracy, saved materials, saved a lot of human errors, but also greatly improved the productivity. Significant improvement, with very real significance.
Sheet metal CNC hydraulic press brake bending machine is stable and reliable, easy to operate, has jog, single stroke, and can maintain pressure. Users only need to equip various molds to bend sheet metal into various shapes. The workpiece can also be used for punching when equipped with corresponding equipment. The main parts of the machine are all made of welded steel plates or forged steel, with high strength, good rigidity and reliable performance.
(1) Frame: The frame frame is composed of left and right uprights, inner braces, fuel tanks, etc. The workbench is seated at the lower part of the uprights and connected.
(2) Slider: The slider is made of a whole steel plate and is connected with the piston rods in the left and right oil cylinders. The two parallel oil cylinders are respectively fixed on the left and right uprights, and the piston drives the slider to move up and down through hydraulic drive. The method is electro-hydraulic servo synchronization mode, controlled by the numerical control system, the flow rate of the two synchronizations can be adjusted automatically, which ensures the synchronization accuracy of the slider, the detection of the slider position is realized by the grating ruler, and the slider is guided by the guide rail device when running.
(3) The convex mechanism of the worktable: located on the right side of the worktable, it is composed of a brake motor, a worm reducer, a screw nut, an inclined spacer, a tie rod and an arc block. The spacer is moved to the left by 40mm. 20mm.
(4) Hydraulic system: The electric motor and oil pump are installed on the top and inside of the oil tank, the pump block is installed on the oil tank, and the two synchronous blocks are installed on the top surfaces of the left and right oil cylinders. In order to ensure that the oil cylinder is filled with oil when the slider descends rapidly, the oil flush valve structure is adopted to improve the stroke speed of the slider and save energy.
Methods to ensure the efficient operation of the press brake bending machine
The press brake bending machine is a workpiece that uses the equipped mold (general or special mold) to bend the metal sheet in the cold state into various geometric cross-sectional shapes. When it develops to 12 axes, the CNC system can automatically realize the sliding depth control, the left and right tilt adjustment of the slider, the front and rear adjustment of the rear stopper, the left and right adjustment, the pressure tonnage adjustment and the slider approaching working speed adjustment and so on. It can easily realize the slide down, jog, continuous, pressure holding, return and stop in the middle, and complete the bending of multiple elbows of the same angle or different angles at one time.
How to solve the problem after it occurs?
First, check whether the mold of the machine is damaged. If the abrasive tool is worn out, then the work of the press brake bending machine will definitely be affected. As long as the mold is repaired, the problem can be solved.
Secondly, if there is no problem with the mold, it is necessary to check whether the parallelism of the slider and the table meets the requirements, and readjust if there is any deviation.
After that, if there is still an error after the above two steps, then check the hydraulic system of the equipment to see if the pressure oil enters the left and right cylinders evenly, if not, adjust it by yourself.
The press brake bending machine includes a bracket, a worktable and a clamping plate. The worktable is placed on the bracket. The worktable is composed of a base and a pressure plate. The base is connected to the clamping plate by a hinge. The base is composed of a seat shell, a coil and a cover plate. Inside the recess of the seat shell, the top of the recess is covered with a cover plate. When in use, the coil is energized by the wire, and after the electricity is energized, the pressure plate is gravitationalized, so as to realize the clamping of the thin plate between the pressure plate and the base. Due to the use of electromagnetic force clamping, the pressing plate can be made into various workpiece requirements, and the workpiece with side walls can be processed. It can meet the needs of various workpieces by changing its molds.
Maintenance methods for the efficient operation of the press brake bending machine:
- The maintenance of the press brake bending machineis not difficult. Check the key parts of the equipment before use, such as the lubrication part to see if it is lubricated well. If not, do it as required. Check whether the safety protection device is abnormal, whether the circuit and grounding are normal, whether the fasteners are loose, and so on.
- During use, observe whether the equipment has abnormal operation, such as unusual noise or vibration. These are all things to pay attention to. If there is an abnormality, it must be stopped.
- After using the equipment, the power supply should be cut off, and all parts should be returned to their positions as required. Clean the equipment.
The above are the very basic maintenance work of the press brake bending machine. Only by doing it according to the requirements can the equipment be in a better state for a long time, so that it can play a better role.