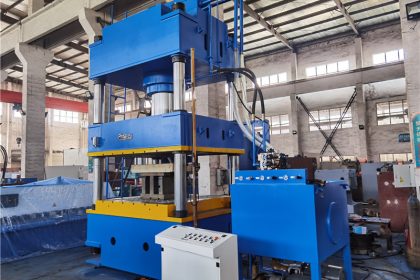
Classification of hydraulic presses and working principle of four-column hydraulic press machines?
Forging itself is related to the forming of steel, so forging hydraulic presses are mainly used in various stamping processes such as stretching, bending, forming, blanking and flanging of steel, especially in the following fields: automotive, household appliances, kitchen utensils, Aerospace, navigation, aviation and other fields.
For example: body, box, front axle, rear axle, frame and other places in auto parts.
Since it is such an important forming equipment, it can form steel into the parts that the factory wants, and the role of the forging hydraulic press is very important. Its structure can be four-column type or frame type.
Forging hydraulic press classification can also be divided into:
- Rapid free forging hydraulic press
- Precision die forging hydraulic press
- Hot die forging hydraulic press
- Multi-sequence die forging hydraulic press
- Multi-directional die forging hydraulic press
- Free forging hydraulic press
There are many categories, but for manufacturers specializing in the manufacture of hydraulic forging presses, as long as the customer needs are stated, the manufacturer’s technical sales will come to a conclusion about what hydraulic forging presses to use. The professional strength has just begun, and the design of the press And the electrical layout is a further sublimation of the professional.
Detailed explanation of the working principle of large tonnage four-column hydraulic press machine
Large-tonnage four-column hydraulic press machinees are constantly updated and innovated in the domestic scientific and technological field. The original large-tonnage four-column hydraulic press machinees can no longer meet the needs of more industries. Therefore, large-tonnage four-column hydraulic press machinees have also produced more types: such as large throats. Bow-type large-tonnage four-column hydraulic press machine, large-throat bow-type large-tonnage four-column hydraulic press machine, fast four-column large-tonnage four-column hydraulic press machine, CNC large-tonnage four-column hydraulic press machine and other equipment series, but different models of equipment, their working principles are the same, then What is the detailed explanation of the working principle of the large-tonnage four-column hydraulic press machine? The editor will tell you in detail today.
Detailed explanation of the working principle of large tonnage four-column hydraulic press machine
In the industry, the working principle of a large-tonnage four-column hydraulic press machine is compared to Pascal’s law, and Pascal’s law refers to a law of hydrostatics. to any point in the stationary fluid. People use this law to design and manufacture fluid machinery such as hydraulic presses and hydraulic drives. And Pascal’s law can only be used in liquids. Let’s take a look at the detailed explanation of the working principle of the large-tonnage four-column hydraulic press machine in stages:
- When the large-tonnage four-column hydraulic press machineworks, the electro-hydraulic reversing valve 6 is energized and the pump 3 sends out oil pressure, which enters the right position of the electro-hydraulic reversing valve 6 through the sequence valve 4, and then enters the upper part of the upper cylinder 12 through the check valve 9. The oil is replenished into the upper chamber of the cylinder through the solenoid valve 7, and the return oil flows from the lower chamber of the upper cylinder, through the back pressure valve 13 of the one-way sequence valve and the hydraulic control one-way valve 14, and flows back through the electro-hydraulic reversing valve 7. Fuel tank: The upper cylinder of the large-tonnage four-column hydraulic press machineaccelerates its downward rapid movement under the action of its own weight, so that a vacuum is formed in the upper chamber of the upper cylinder in an instant, and the oil in the replenishment tank will be sucked into the upper chamber of the upper cylinder through the hydraulic control check valve to eliminate Vacuum, keep the upper cylinder moving down quickly.
- When the upper cylinder of the hydraulic press drives the upper mold and the lower mold to close the mold, the oil continues to be input into the upper cavity of the upper oil cylinder, the pressure of the upper cavity of the oil cylinder rises, and the hydraulic control check valve at the replenishment tank is closed, cutting off the supply of the replenishment tank. oil, so that the downward speed of the upper cylinder 12 begins to slow down, and the pressure in the upper chamber of the cylinder continues to rise. When the set value of the pressure relay 10 is exceeded, a signal will be sent to control the electro-hydraulic reversing valve 6 to switch to the neutral position to cut off the cylinder 12. After the oil supply to the cavity, the upper cylinder of the hydraulic press stops the motion system, and starts to maintain the pressure for about 40s; after the completion of the large-tonnage four-column hydraulic electro-hydraulic reversing valve 6, the left position is turned on, and the pressure oil from the pump 3 passes through the sequence valve 4, through the electro-hydraulic The left position of the reversing valve 6, through the hydraulic control check valve 14 and the back pressure valve 13, enters the lower chamber of the upper oil cylinder 12, pushes the oil cylinder to move upwards, while the solenoid valve 7 is switched to the left position, and the oil tank is replenished to accelerate the return; The return oil in the upper cavity of the oil cylinder 12 flows back to the replenishment tank 11 through the hydraulic control one-way valve, and finally the upper cylinder can quickly return to its original position.
- When the neutral position of the electro-hydraulic reversing valve 6 and the right position of the electro-hydraulic reversing valve are connected, the pressure oil from the pump 3 enters the lower cavity of the lower cylinder 16 through the left position of the electro-hydraulic reversing valve of the hydraulic press, and returns to the lower chamber of the lower cylinder 16. The oil flows from the upper chamber of the lower cylinder 16 through the left position of the electro-hydraulic reversing valve into the oil tank, and the lower cylinder pushes up the workpiece; after the workpiece is taken out, the right position of the reversing valve of the large-tonnage four-column hydraulic press machinestarts to work, and the pressure oil enters the lower cylinder In the upper chamber of 16, the return oil in the lower chamber of the lower cylinder flows into the oil tank through the right position of the valve, and the lower cylinder moves downward to return to its original position; the valve 13 can prevent the oil in the upper chamber of the upper cylinder 12 from flowing back when the pressure is maintained, and the travel switch 15 is used to control the limit positions of the upper and lower cylinders. At this time, the pressure gauge displays the pressure values of the upper and lower cylinders and the entire system of the large-tonnage four-column hydraulic press machine.