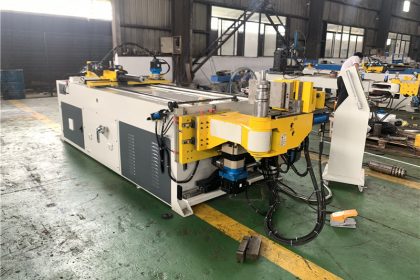
How to improve the product efficiency of CNC pipe bending machine for pipe processing equipment
How to improve the high-efficiency transformation of CNC pipe bending machine system
In the field of pipe processing machinery, the main sales force of CNC pipe bender equipment and pipe cutting machines and pipe shrinking machines is still relying on the hydraulic system as the core power unit of the machine. In the past two decades, we have been constantly improving and improving Metal circular sawing machine, pipe end forming machine and single-head CNC pipe bending machine equipment tube bending, cutting, pipe end forming and other processing technologies.
In the past ten years, due to the continuous upgrading of the technological revolution, the automatic numerical control pipe bending machine and the numerical control operating system man-machine interchange and other technical fields have been updated and upgraded, and the numerical control numerical control pipe bending machine has become more and more advanced and convenient. , For some difficult pipe bending processing, as well as the upgrade of pipe cutting machine equipment with CNC numerical control operating system small section cutting, it also achieves more high-precision and high-efficiency production. We use our CNC pipe bender on the exhaust pipes of buses and automobiles. Because the previous hydraulic CNC pipe benders were still unable to achieve the processing accuracy, automatic feeding and automatic corner positioning, these are all relying on manual measurement to complete Therefore, to a large extent, it is impossible to achieve the improvement of high precision and efficiency. However, the development of CNC technology revolution in the past ten years has bid farewell to the traditional CNC pipe bending machine in the past, and the current hydraulic CNC pipe bending machine Compared with the hydraulic CNC pipe bender 20 years ago, there are still great advancements in many technologies.
Introduction to hydraulic CNC pipe bender accessories: About the hydraulic cylinder material and transmission principle of the hydraulic CNC pipe bender. The materials of hydraulic cylinders are relatively hard, and the materials are also seamless steel pipes.
The transmission of the hydraulic CNC pipe bender is mainly driven by hydraulic oil to drive the piston. The internal structure of the piston rod is sealed by the sealing ring and wear strip. Because the hydraulic oil is relatively low in density, the internal structure of our piston is very precise. The material of the sealing ring Generally mainly imported. The front end of the piston rod is equipped with a rack. The piston moves forward and backward through the rack and pinion. The hydraulic solenoid valve transmits oil pressure and pushes the piston to achieve bending, clamping, and so on.
The servo motor in the automatic CNC pipe bending machine plays a vital role in the equipment. The automatic CNC pipe bending machine is not like the hydraulic CNC pipe bending machine because the bending power depends on the hydraulic pressure, and their entire movement relies on the servo motor. To provide power. Therefore, the precision and efficiency of a fully automatic CNC pipe bender depends on the cooperation of our servo motor. Therefore, in adjusting the servo motor, the technical difficulty is also very high.
Metal circular sawing machine and accessories and metal circular saw blade introduction; about metal circular sawing machine and pipe cutting machine, we usually use the process, mainly for the cutting and processing of pipes and metal special-shaped pipes, but due to the different materials of the pipes, the Whether the circular saw machine can work well and the best cutting efficiency also needs to be determined according to the metal circular saw blade. For the different wall thickness of the pipe material, it is particularly important in the selection of the metal circular saw blade. Choose the rigidity of the high-speed steel circular saw blade according to the wall thickness to match the saw teeth and the material.
The good performance of the servo is the key to the normal operation of the entire equipment. By adjusting the parameters, the servo motor runs in the best state to ensure the normal operation of the entire equipment. Due to the difference of the transmission mechanism, in order to ensure the speed and accuracy of the equipment, each axis needs to appropriately adjust the number of pulses required for the final output end to make one revolution, but the two axes that realize the interpolation need to ensure that the number of pulses is complete Similarly, this problem can be easily solved by setting the electronic gear ratio of the servo motor.